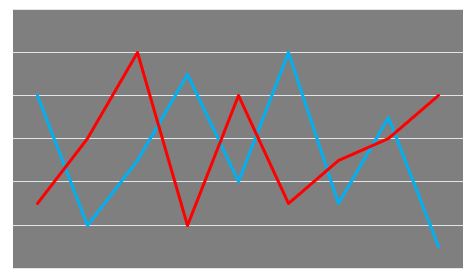
Every company deals with performance challenges and volatility. It's the one thing that's universal to us all, mistakes occur. Performance is cannot be 100% expected without fail all the time. If you read this, every one of you are dealing with at least one of the following:
- Unreliable production lines/facilities
- Transportation reliability challenges
- Customer order volatility
- Supplier challenges on finished SKUs or materials for production
- Warehouse reliability
- Personnel or process inconsistency
We've already discussed the Demand/Order variation last week, however the fact remains that most companies focus primarily on carrying more inventory to pad for these reliability challenges rather than to attack the root causes themselves.
Do you have transparent measurements in place with a standard cadence of communication on all? Between downtime, capacity utilization, OEE, run rates, schedule adherence, etc. are you able to isolate all measurements down to the source? Tactically root cause deviation and quickly solve?
Does your organization have visibility to the carriers/lanes with the worst on time performance, highest percentage of equipment failures? Do you eliminate problematic carriers in either performance on or for simply not providing root causes on their own failures?
What about your fill rates on goods/materials received from outside suppliers? Received on time?
Warehouse Turns?
Can you measure your planning and scheduling deviations down to the individual responsible for it? Do line supervisors know their line's KPI's on reliability?
These metrics and creating a culture of continuous improvement are incredibly important. Inventory is a band-aid. A culture of fixing the problem rather than band-aiding service with inventory is absolutely necessary if you're going to reset your company and team mindsets on this subject.
Transparent measurement of variability throughout the supply chain is necessary. Confidence that key players are solving the root issues is a must.
Culture, data, and responsiveness. People, process, and tools. Let us help, inventory is seldom the answer.